If you're going to use plywood for any construction or do-it-yourself project, you should know the basics of the material. With wood, a little bit of knowledge goes a long way and can be the difference between a successful and unsuccessful project.
What is Plywood?
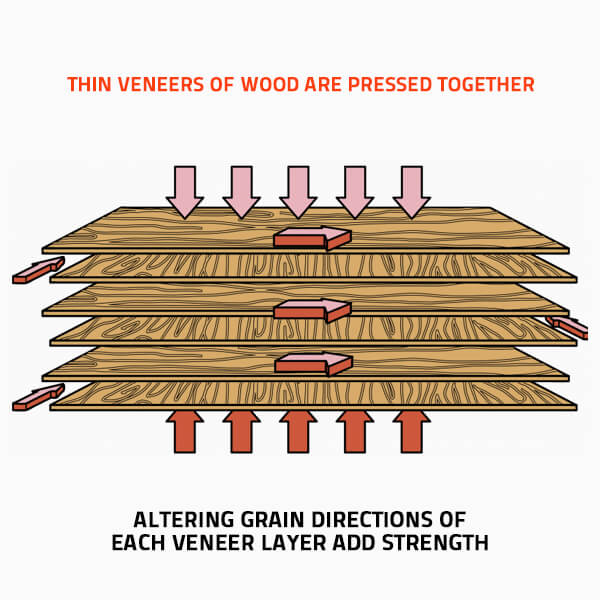
The simplest definition of plywood is a flat sheet of wood veneers that have been bonded together. The word "ply" refers to plywood's multiple thin layers and comes from the French verb for "fold", which is "plier".
How is Plywood Made?
A form of engineered wood (wood derivatives manufactured by binding or fixing resin and wood fibre sheets together), plywood always has at least three layers of veneers. Different tree species and glues are used to create different final products, and in all cases, they are finished with a bonding process that involves heat and pressure.
The number of layers, or plies, is also always odd to properly balance the sheet and reduce the risk of warping. The plies in some sheets may all be at right angles to each other, or – if there are more layers – they may be at stepped angles of 45 degrees, which gives strength along multiple axes.
Either way, this method of alternating the angles of the grain is known as cross-graining or cross-lamination and gives plywood its durability and strength. Cross-graining reduces wood expansion and shrinkage, improves dimensional stability, lessens the risk of splitting when the material is nailed at its edges, and makes the panel's strength consistent in all directions.
A Brief History of Plywood
Since plywood is so obviously manufactured and used for several modern-day applications - such as large-scale cabinet building - many people think it's a relatively new material. That's an understandable assumption, but it couldn't be more wrong.
The process of cross-lamination to create a plywood-like material is shown on a carving found in Thebes and dating back to Ancient Egypt! Ancient Greece is also known to have used this bonding technique. In 1797, noted British naval architect and mechanical engineer Sir Samuel Bentham applied for several patents for machines that produced veneers.
In his patent applications, Bentham gave the first written description of what we now know as plywood – he outlined the concept of laminating layers of veneer and glue to create a thicker piece. Roughly 50 years later. Nobel Prize creator Alfred Nobel's father, Immanuel, saw the potential of laminated wood for industry.
Nobel Senior invented the rotary lathe, which is used, among other applications, to turn pieces of wood and thus remove thin sheets from them. Picture peeling an apple with a sharp knife, and you've got a good idea of the process. A description of rotary lathe veneer production was entered into an 1870 edition of a French dictionary, so it's safe to assume that this kind of manufacturing was established in France by that time.
Plywood made its way to the United States in 1865 and was used in industrial production shortly thereafter. The first standard-sized sheets were introduced to the US markets in 1928 to be used as a general building material. By this point, the sheets were no longer considered elegant and refined. Rather than being associated with elite, bespoke pieces, they became linked with cheap mass production.
When water-resistant, high-quality synthetic glues were invented in the 20th century, plywood was given a whole new lease on life. Most significantly, it was essential to the construction of barracks, boats, weapons and even aircraft in the Second World War. Geoffrey de Havilland's famous multi-role mosquito, often affectionately called The Wooden Wonder, used the material for its wing surfaces, bulkheads, fuselage and other sections.
Plywood Types and is Applications
But let's get back to the present; what is plywood used for today?
Simply put, almost anything!
Depending on the type of wood and glue, along with the sheet's grading, it can be everything from a blank canvas replacement for artists to the material used for playground equipment.
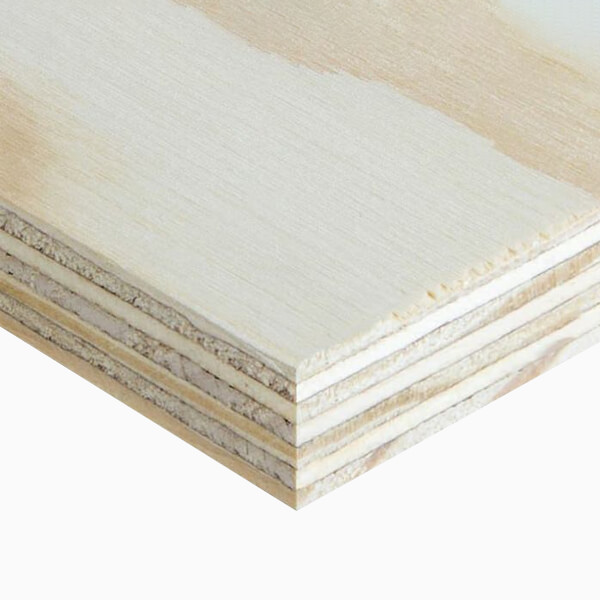
Softwood plywood, typically made of Douglas fir, cedar, spruce, pine, or redwood, is ideal for constructing wind-bracing panels, floors, roofs and walls. In addition, it works well for fencing and vehicle internal bodywork and for making boxes and packaging.
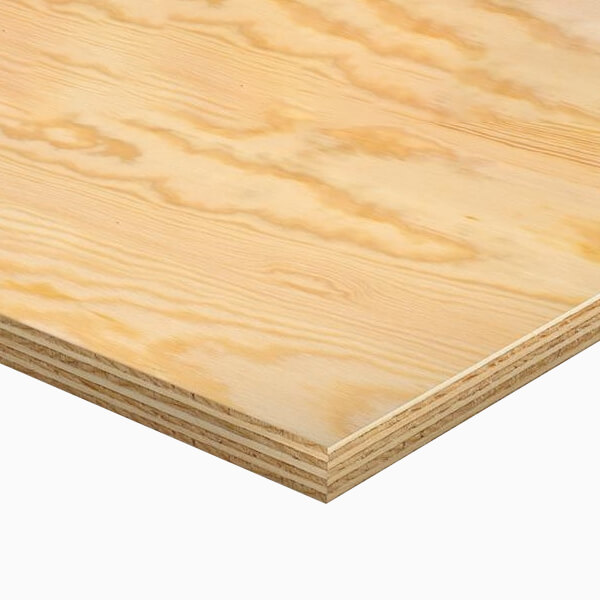
Tropical plywood is mainly supplied by Malaysia and Indonesia, along with other countries in Southeast Asia. Made of mixed tropical timber species, it's used in many everyday applications, including economic house construction, structure panels and smaller do-it-yourself projects.
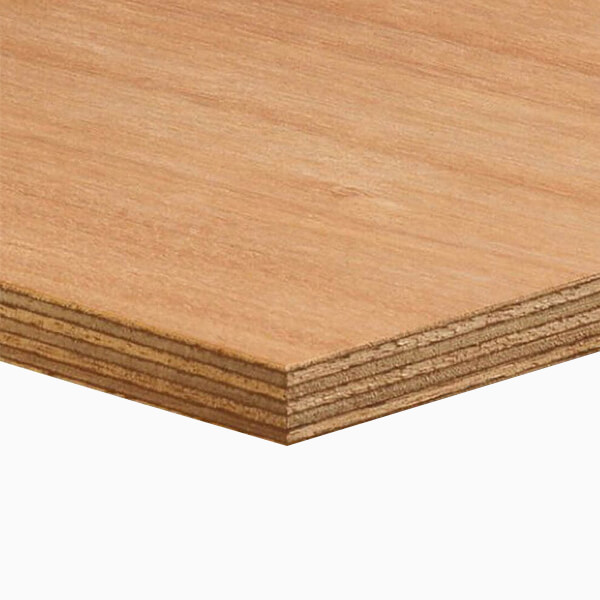
Hardwood plywood is made of dicot trees like Oak, Mahogany and Beech, and is used for especially demanding environments. For instance, heavy-duty floors and walls in factories, containers and transport vehicles are often made from the material. Wind turbine blades and the insulation boxes on liquified natural gas carriers are two other prime examples.
The accurate, uniform thickness of hardwood plywood also makes it a top choice for die-cutting boards, high-end loudspeaker construction, signs and fences for outdoor advertising, sports equipment, musical instruments and furniture.
Plywood Gradings
Plywood is graded according to several variables. The grade can have a single letter, indicating the same grade applies to the front and back, or two letters separated by a slash when the front and back are different grades. The grading system is outlined below.
- A: Practically free from all defects on both sides.
- A/B: Face veneer is almost completely defect-free; reverse veneers display a few discolourations or small knots.
- A/BB: Face veneer almost perfect; reverse side permits joints, large knots and plugs.
- B: Veneers on both sides have a few discolourations or knots.
- B/BB: A few knots or discolourations on face veneer; joints, plugs and large knots permitted on the reverse side.
- BB: Large knots, plugs and jointed veneers are permitted on both sides.
- C/D: A structural plywood grade that means the face has filled-in defects and knots, while the reverse might have some which have not been filled in. Neither side has an appearance grade, and neither is sanded smooth. Often, the C/D grade is used for sheathing a building's surfaces before it is covered with flooring, siding or another product.
- WG: All broken knots are plugged, but the only guarantee on this grade is that it has been well glued.
- X: All defects, including cracks, knots and knotholes, are permitted.
- WBP: Weather and Boil Proof plywood.
What is WBP Plywood?
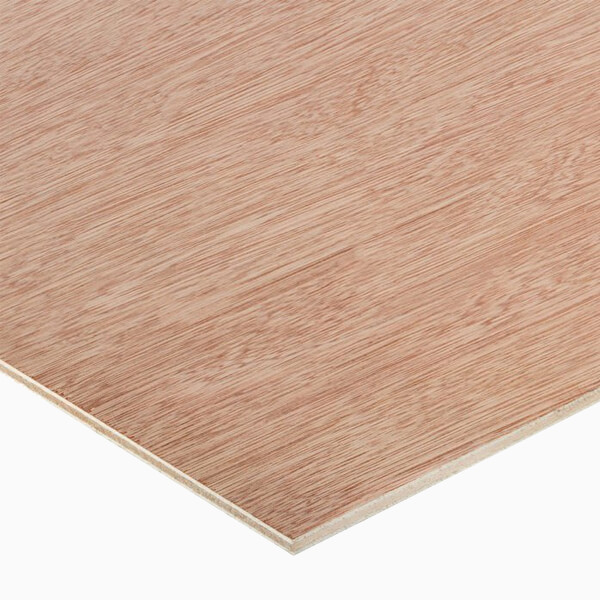
Weather and Boil Proof plywood is the most durable type, because of the melamine or phenolic resin used in its bonding process. Since it is so strong, WBP plywood is the only category the United Nations Food and Health Organisation recommends without reservation for exterior use.
The WBP rating is a glue standard developed in the United Kingdom and set down in British Standards Institution standard 1203:1963. Phenolic resin WBP can withstand being submerged in boiling water for one to three days; melanin WBP can do so for 10 to 20 hours. The exact length of time depends on the grade of the wood veneers and the glue being used.
What is Marine Plywood?
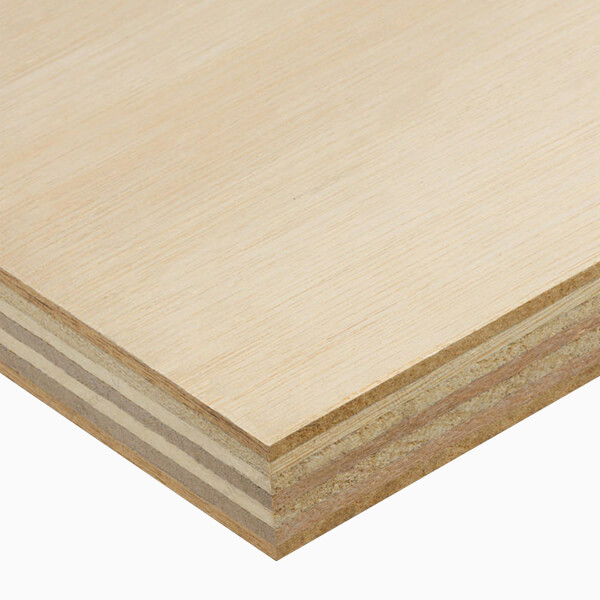
Marine-grade plywood is not fully waterproof as its name might suggest, but its waterproof glue makes it highly moisture and water-resistant. Specifically made of Douglas fir or Western larch, marine plywood may have knots, but will never have knotholes. Lightweight-strong and almost defect-free, it's perfect for outdoor furniture projects, especially in coastal areas, boats and boat parts.
Advantages of Plywood
- Incredibly flexible.
- Split edges due to nails are reduced.
- Material strength is increased.
- Minimal expansion and shrinkage.
- Low risk of warping.
- Plywood furniture is lighter to transport than solid wood pieces.
- Plywood is economical to use.
Disadvantages of Plywood
- Risk of long-term insect or water damage, although this can be minimised with a treatment of the veneers.
- Sculpting to surfaces is not always easy.
- Not as durable as wood.
- If not painted well, the surface of the plywood can peel off.
Make Sure Your Plywood is Legitimate
Once you've decided what type of plywood you want to use, you're ready to go! Just make sure that it is certified as being ethically produced, with a seal of approval from the Forest Stewardship Council or other organisations that check the manufacturing sustainability.
Find all the best above-board plywood at Buildworld for projects you can feel good about in every way.
Related Articles
Category
Doors & WindowsPosted On
27th February 2025